Overview
Tensile strength, yield strength, elongation, and reduction of area are all belong to mechanical properties of alloys. They determine the strength and plasticity of alloys. Different applications often require alloys with different mechanical properties. In this article, we detail the definitions of these mechanical properties and the factors that determine the mechanical properties of alloys. This can help you make better decisions when selecting materials.
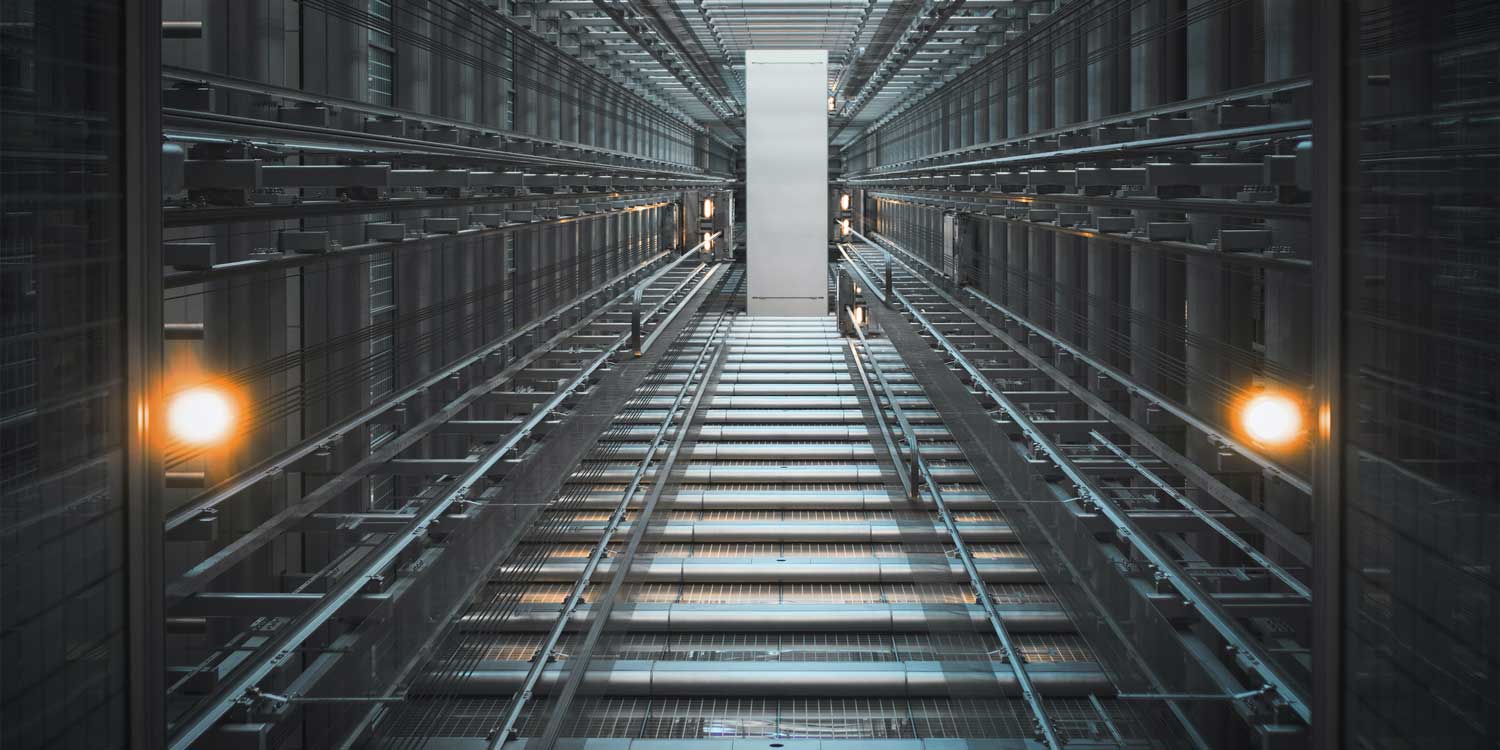
What are Mechanical Properties
Mechanical properties refer to the mechanical characteristics of alloy materials when they are subjected to external forces. Commonly used mechanical properties include tensile strength, yield strength, elongation and reduction of area. Among them, the tensile strength and yield strength mainly reflect the strength of the alloy. The elongation and reduction of area reflect the plasticity of the alloy. The higher the strength of the alloy, the greater the external force it can resist. Alloys with higher plasticity are less prone to cracking and more resistant to bending. In general, the higher the strength of an alloy, the lower the plasticity.
The essence of mechanical properties is the ability of alloy to resist deformation. Microscopically, it is the ability to resist sliding between alloy crystal layers.
Sliding Between the Layers
Test Methods for Mechanical Properties
To know the mechanical properties of an alloy, it is generally necessary to perform tensile tests on the alloy. Tensile tests need to be performed according to specific standards. The more commonly used standard is ASTM E8.
Before the tensile test, it is necessary to make the corresponding specimen according to the standard. Some common specimen shapes are listed below:
Common Specimen Shapes
After the specimen is prepared, the tensile test can be started. At the beginning of the tensile test, the two ends of the sample will be clamped by two jigs respectively. The jigs then pull the specimen in two different directions. During this process, the tensile force of the jig will continue to rise. Until the material is broken, the tensile test is complete. Afterwards, the tester will record the mechanical properties of the material based on the data during the test. The mechanical properties recorded by the tensile test are also called tensile properties.
Classification of Mechanical Properties
Tensile Strength
Tensile strength refers to the ability of a material to resist fracture during stretching. The unit is MPa. In the tensile test, the moment the material is broken, the tensile force applied to the alloy material will be recorded. The value of dividing this tensile force by the original cross-sectional area of the alloy specimen is the tensile strength.
Tensile Strength
In practical projects, many materials need to withstand high stress. If the material breaks during use, it is likely to cause serious problems. Therefore, tensile strength is a very important mechanical index in engineering.
For wires, tensile strength is the only reference in most cases. Among them, spring wire has the highest requirement for tensile strength. They are often used to make springs that need to withstand long-term compression or tension.
Yield Strength
Yield strength refers to the ability of a material to resist deformation during stretching. In a tensile test, the material does not undergo any deformation at lower tensile forces. When the tension increases to a certain level, the material begins to deform. The yield strength of the material is obtained by dividing the tensile force at this time by the original cross-sectional area of the specimen.
Yield Strength
Since the material first deforms and then breaks during the process of increasing the tensile force, the yield strength is often less than the tensile strength for the same material.
In some applications, materials are required not to deform when subjected to stress. At this time, the yield strength of the alloy becomes the key reference index.
Elongation and Reduction of Area
Elongation reflects the degree to which a material deforms during stretching. During a tensile test, the material deforms before breaking. The elongation is obtained by dividing the increased length of the material after breaking by the original length of the material.
Due to the deformation of the material after fracture, the cross-sectional area of the fracture will be smaller than the original cross-sectional area of the specimen. The reduction of area is obtained by dividing the reduction in cross-sectional area by the original cross-sectional area of the specimen.
Elongation and Reduction of Area
Both the elongation and the reduction of area can be used to judge the plasticity of the material. The greater the elongation and the reduction of area, the better the plasticity of the material.
In some applications that require bending to process materials, materials are required to have good plasticity. At this time, elongation and reduction of area are important reference indicators.
Factors Determining Mechanical Properties of Superalloys
Chemical Composition
Chemical composition is the fundamental factor determining the mechanical properties of alloys. If the strength of a material itself is very low, it is difficult to achieve very high performance even through subsequent processing.
According to classification, superalloys are mainly divided into solid solution strengthened alloys and precipitation strengthened alloys. Of the two, precipitation strengthened alloys can be subjected to an aging treatment process. Its strength is much higher than that of solid solution strengthened alloys.
For solid solution strengthened alloys, the strength of the alloy often depends on the solid solution elements in the alloy. Among them, elements that play a significant role in solid solution strengthening include molybdenum, niobium, tantalum, tungsten, and cobalt. The greater the content of these elements, the higher the basic strength of the solid solution strengthened alloy.

For precipitation strengthened alloys, the strength of the alloy depends on the number of strengthening phases. The amount of strengthening phase is related to the amount of precipitation strengthening elements. Common precipitation strengthening elements are aluminum, titanium, niobium, and tantalum. In general, the greater the amount of these elements, the stronger the precipitation strengthened alloy.

In addition, some elements (such as carbon) will exist between alloy crystals to form a barrier to displacement. They can also further increase the strength of the alloy.
There is also a special superalloy -- dispersion strengthened alloy. It mainly increases the strength of the alloy at high temperature by adding yttrium oxide.

Processing
After processing, the grains of the alloy are stressed and deformed. This deformation increases the irregularity of the crystals and at the same time increases the contact area between the crystals. This leads to an increase in the intercrystal force, which impedes the sliding displacement of the crystal. The macro performance is that the strength of the alloy is improved. This phenomenon is called work hardening.
Process of Work Hardening
Most processing results in work hardening. Such as: hot rolling, cold rolling, cold drawing, machining, surface polishing, etc. Most of the time, the alloy is processed several times in order to achieve the required dimensions of the product. The more processing times, the higher the strength of the alloy.
Heat Treatment
Heat treatment is a common way to modify the mechanical properties of alloys. It can both increase and decrease strength.
The alloy undergoes work hardening after machining. At this time, the alloy has high strength and low plasticity, and is very easy to break. In order to improve the plasticity of the alloy, it is generally necessary to anneal or solution treat the alloy. This treatment requires the alloy to be heated. Alloy crystals tend to recover to a certain extent during the heating process. This recovery weakens the work hardening effect of the alloy. Reduces the strength of the alloy and improves plasticity.
Process of Heat Treatment
For precipitation strengthening alloys, the strength can be improved by aging treatment. Aging treatment often requires keeping the alloy at a certain temperature for several hours. During the placement process, elements such as aluminum and niobium in the alloy will precipitate out of the matrix and form a precipitation strengthening phase. There is a great hindrance to the displacement sliding between the strengthened relative matrix. After aging treatment, the strength of the alloy will be greatly improved.
Crystal Phase
In addition to chemical composition, processing and heat treatment, crystal phase is also a factor in determining the mechanical properties of superalloys. For some superalloys, if the heat treatment process is not handled properly, harmful phases are easily precipitated in the alloy. This detrimental phase can greatly affect the tensile properties of the alloy. Alloys even cannot compensate for this effect by other means.
Defect
Defects are also a factor affecting the mechanical properties of the alloy. If serious defects such as cracks appear in the alloy, the tensile properties of the alloy will be greatly reduced. Therefore, defects should be avoided as much as possible during the production of alloys.
Conclusion
Mechanical properties refer to the performance of an alloy when it receives an external force. Among them, tensile strength, yield strength, elongation and reduction of area are the most commonly used. They are also known as tensile properties. They determine the availability of materials in the actual project.
Tensile properties can be measured by tensile testing. Corresponding specimens need to be prepared before the tensile test.
Chemical composition, processing, heat treatment, crystal phase and defects are the main factors affecting the tensile properties of alloys. These factors can be exploited or avoided during production to achieve the desired properties of the alloy.
We strictly follow the standards and customize superalloy materials according to your needs. If you have needs, you can contact us.