Overview
Fatigue is a phenomenon of alloy. It is caused by stress in different sizes and directions. Fatigue can lead to a break in alloy.
In this article, we will describe the principle of fatigue in detail. Together with the factors that affect the fatigue strength of alloy.
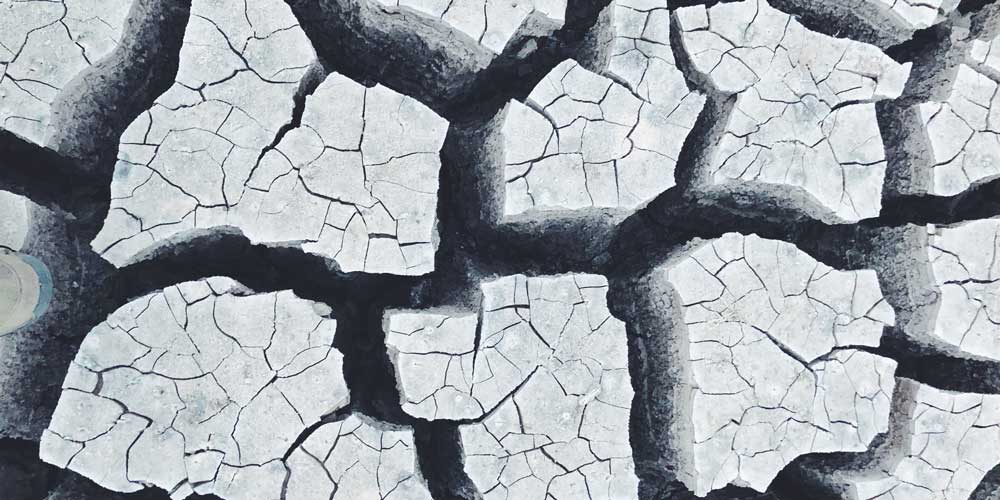
What is Fatigue
In some applications, alloys are subjected to forces of different magnitudes or directions. Very often, such forces act alternately on the alloy.
For example, in aero engines, turbine blades are periodically subjected to centrifugal forces in different directions during rotation.
Although sometimes this force is less than the yield strength of the alloy, the repeated alternation of forces makes the alloy susceptible to small deformations caused by concentrated accumulation of stresses at one point. Eventually, the alloy cracks and leads to fracture. This is the fatigue phenomenon of an alloy.
The figure below shows the principle of fatigue phenomenon.
The Principle of Fatigue
The Three Processes of Fatigue
Generally speaking, fatigue goes through three processes.
The first process is the fatigue hardening or softening process. During this stage, microstructural and organizational changes occur in the alloy. Eventually there will be a concentration of small deformations at a certain place.
The First Process
The second process is the formation of microcracks. Cracks are formed mainly on the surface at the micro-deformation. This stage leads to a loosening of the surface structure of the alloy at the point of deformation. The conditions are created for the fracture of the alloy.
The Second Process
The third process is the fatigue crack extension process. The micro cracks formed in the second process are interconnected to form the main crack, which further expands with alternating stresses and causes fatigue fracture of the material.
The Third Process
Classification of Fatigue
Depending on the magnitude and alternating frequency of the stresses received by the alloy, fatigue can be divided into two categories: high-cycle fatigue and low-cycle fatigue.
In the process of fatigue occurrence, some of the forces acting do not change regularly. However, in most cases, the acting forces vary regularly and periodically, and such forces are called cyclic stresses. The most common variation pattern is a sine wave.
Sine Wave
The figure above shows the shape of a sine wave. The force varies continuously according to a certain cycle of high and low. The height of the wave represents the magnitude of the force, and the density of the wave in the horizontal direction represents the frequency of change of the force, i.e. the number of cycles.
High-cycle fatigue is characterized by a small force and a large number of cycles.
High-cycle Fatigue
Low-cycle fatigue is characterized by a high force and a low number of cycles.
Low-cycle Fatigue
The following figure compares the difference between high-cycle and low-cycle fatigue.
The Difference between High-cycle and Low-cycle Fatigue.
Factors Affecting the Fatigue Strength of Alloys
In practical projects, we have to consider how to minimize the adverse effects from fatigue. Therefore, it becomes crucial to study the factors that affect the fatigue strength of the alloy.
Surface
Since fatigue cracking tends to occur on and near the surface of the alloy, surface condition is an important factor in fatigue strength. For some alloy applications, machining destroys the surface integrity of the alloy, causing surface roughness and causing surface work hardening. These factors all contribute to a reduction in fatigue strength.
Shot peening is an effective solution to this problem. It is very beneficial in improving fatigue properties. At the same time, chemical heat treatment (such as surface coating, etc.) can strengthen the surface and improve the fatigue strength of superalloys. In addition, the fatigue strength can also be improved by surface grain refinement.
In short, all the measures and methods that are conducive to improving the surface finish and surface strengthening are generally conducive to fatigue strength improvement.
Notches
Some alloy parts are designed to be notched. Such notches can lead to stress concentrations. This facilitates the sprouting of fatigue cracks. Therefore, the fatigue strength of notched parts is generally reduced. Therefore, it is necessary to consider the stress concentration during design.
The notch radius significantly affects the fatigue performance of the alloy. The smaller the notch radius, the greater the fatigue strength reduction. This is because as the notch radius decreases, the stresses become more concentrated. This results in a significant reduction in fatigue performance.
Temperature
The effect of temperature on the fatigue of the alloy is more pronounced. The fatigue strength is higher at lower temperatures. And as the temperature increases, the fatigue strength gradually decreases. This law is similar to the effect of temperature on the tensile strength of the alloy.
At high temperatures, the fatigue strength is lower than the fatigue strength at room temperature because the strength of the alloy is lower than the strength of the alloy at room temperature.
On the other hand, the high temperature plasticity of the alloy is significantly better than room temperature. The increased plasticity reduces the stress concentration at the notch. And because the alloy can be dynamically recovered at high temperature, the degree of damage to the alloy can be reduced. Therefore, the effect of notching on the fatigue strength of the alloy at high temperature is significantly lower than that at room temperature.
In addition, the increase in temperature increases creep and thus also reduces fatigue strength.
Frequency
For most alloys, the frequency of stress cycles has little effect on the fatigue strength. However, if the frequency is too low (especially below 60 cycles/minute), the fatigue strength will be slightly reduced. This effect increases when the temperature increases. This is because in addition to the effect of increasing temperature on the structure, it also increases creep.
Mechanical Properties
With different alloy grades (chemical composition), the strength and plasticity are also different. At the same time, the same grade of alloy also has a different microstructure due to different heat treatments and processes, resulting in different mechanical properties.
Both the strength and plasticity of the material affect the fatigue strength. For an alloy with stable organization, the higher the tensile strength, the higher the fatigue strength. The higher the plasticity, the lower the notch sensitivity.
Grain Size
The reduction in grain size of high superalloys usually favors the increase in fatigue strength. Within the alloy, crack expansion requires the breaking of intergranular forces. The smaller the grain size of the alloy, the greater the number of grains. The slower the crack propagation will be.
Microstructure
In addition to grain size, the structure of superalloys also includes the solid solution strengthened state, precipitation strengthened state, etc., all of which can have a significant effect on fatigue strength. For precipitation strenghened superalloys, elements precipitate out of the matrix during the aging treatment, which reduces the solid solution strengthening effect. Therefore, the fatigue strength of the alloy in the precipitation strengthened state will be reduced.
Conclusion
Fatigue is caused by changing forces concentrated in one part of the alloy. Fatigue can further lead to fracture of the alloy and therefore needs to be avoided.
We produce high quality nickel alloy products and can be contacted for any of your needs.